UCR American Solar Challenge
June 2017 - June 2018
Mechanical Team Leader in charge of the design of mechanical requirements stated by competition officials. Subsystems chassis, steering, safety features, suspension and areo-shell. Worked through the manufacturing of the chassis and suspension system.

Chassis Design
My Background
Our solar car features a 4130 chromoly space frame in accordance will all safety requirements put forth by the competition such as being able to withstand 5G impacts at critical points.

Chassis Size
My Background
Our team decided to go for a practicality and comfort over compactness and uniqueness. This done to ensure a safer design and for potential reuse of the vehicle for the same or similar competitions or student projects. All of the teams safety features were approved by the competition commity.
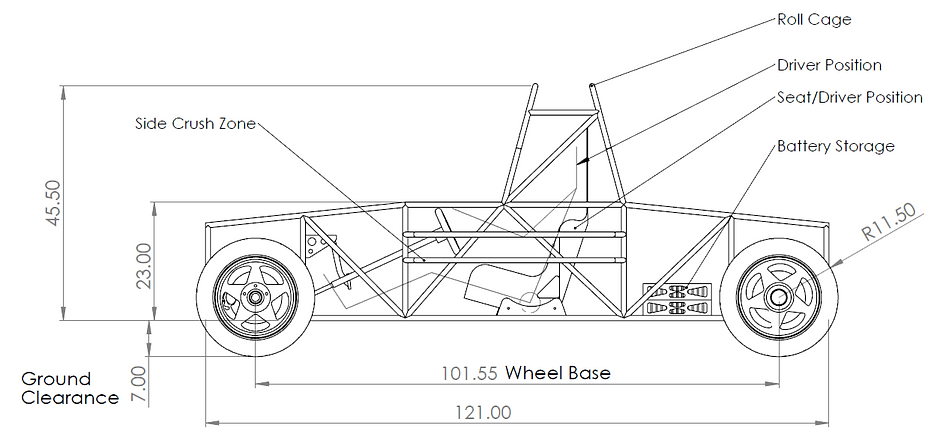.png)

Chassis Analysis
My Background
Analysis was conducted using SolidWorks Simulation as well as on Ansys for confirmation. 5G impact loads were tested on the front, rear, sides, top and angled front locations.

Chassis Alternatives
Contingency Plans
Alternative aluminum chassis design were also designed and tested. These designs were not going to be used as aluminum is more expensive, weaker and harder to weld than steel. However its lower weight makes it a great choice for future teams to expand upon. The final aluminum design was lighter and more compact than the steel design however estimates had it at four times more expensive.

Chassis Construction
Contingency Plans
Due to the fact that the Solar Car Project was brand new, machine shop access was not attainable and a room to store the chassis could not be acquired in time. Thus the construction of the chassis and suspension components were outsourced to a local machine shop.

Suspension Design
Standard Suspension Geometry Design Focused on a smoother ride for long distance.

Suspension Design
Double A-Arm Suspension
.png)
Suspension Design
Standard Suspension Geometry Design Catering to Grand Touring
.png)
Aero-Shell Design
My Background
The Aero -Shell was designed primarily with the constraint of fitting the maximum number of solar cells allowed while remaining under the overall vehicle size limits. Additionally the design offered minimal drag to improve efficiency.
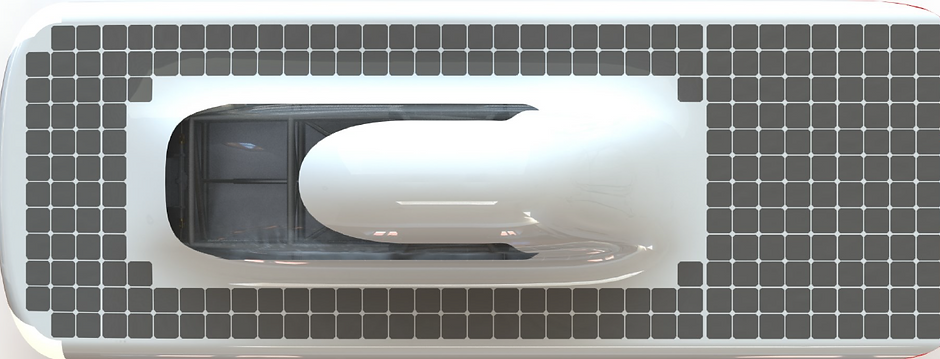.png)
Aero-Shell Analysis
Coefficient of Drag and Down Force
Numerous design variations were analyzed to determine the optimum shape and features of the aero-shell. Important parameters included the coefficient of drag and reduction of frontal area to reduce drag force.
.png)